User:Jrkenti/TST-WI-061
Appearance
AKR Flash Assembly Work Instruction explains the proper way to assemble a Flash reactor.
Materials
[edit]This section describes the tools and the consumables needed to execute this work.
Tools
[edit]
Consult with a lead or engineer if you are unsure of the proper tool for any particular step.
- Small Torque Screwdriver – 3 in-lbs (for control board screws)
- Medium Torque Screwdriver – 10 in-lbs (for single clamshell screw)
- Large Torque Screwdriver with 11/16” hex socket - 13 in-lbs (for NPT fittings)
Inputs
[edit]- Parts per DEV-BOM-005
Outputs
[edit]- Assembled Flash Reactor, ready for testing according to TST-WI-062
Process
[edit]Klaran WS (Flash) units can be assembled one at a time start to finish, or sub-assemblies can be made and each reactor can involve just assembling the completed sub-assemblies. If building sub-assemblies, build 20 of each sub-assembly before starting any final assembly.
Prepare
[edit]- Collect 20 AKR reactors from finished goods
- Sit down at a computer work station with a label printer (loaded with white 0.75x2.25" stickers), and with ActiveBarcode properly installed.
- Open & log into Unipoint and download a new copy of the Flash traveler (TST-F-049) from Unipoint. A VBA macro should immediately begin, follow its instructions.
- SCAN AKR serial numbers onto log sheet
- SELECT the correct power adaptor in the dropdown on the traveler
- PRINT the log sheet & barcodes
NPT Fitting Sub-Assembly
[edit]- UNBOX the AKR, discard the bubble bag, recycle the box and set aside the ESD bag
- Using a section of ¼” tubing with some print on it, WRAP ¼” wide Poly-Temp HD PTFE Tape around the tube 5 times by spinning the tube as shown. Use the print on the tubing as a guide to count the turns of the tubing.
- TEAR the tube and tape away from the roll with a quick tug.
- APPLY the PTFE tape to the middle of the NPT threads on the AKR in a clockwise direction when viewing from the open end of the NPT fittings, as shown.
- REPEAT the above steps for both NPT fittings on the AKR.
- Hand TIGHTEN two NPT to ¼” PTC fittings to the AKR ports
- SNUG fittings using the large torque screwdriver with 11/16” socket set to 13 in-lbs. Continue turning the screwdriver slowly until it clicks several times in a row.
Tubing PTC Sub-Assembly
[edit]- PUSH one PTC coupler onto the end of the tubing
- The tubing must seat fully into the PTC fitting
- PUSH one PTC coupler onto the end of the flow sensor:
- The orientation is critical
- The PTC fitting must be on top, with the arrow on the flow sensor facing down
- The flow sensor must seat fully into the PTC fitting
- PUSH the tubing into the port closest to the metal end of the AKR:
- The tubing must seat fully into the port
- PUSH the flow sensor into the port furthest from the metal end of the AKR
- The flow sensor must seat fully into the port
Housing and Control Board Sub-Assembly
[edit]![]() | ESD REMINDER The steps described here require the user to be properly grounded to eliminate electrostatic discharges. Electrostatic discharges (ESD) can irreversibly damage electronic devices, including our LEDs. |
- PLACE one #4 x 5/16” self-tapping screw through the hole in each corner of the control board
- PLACE the control board with the black external port facing out of the rectangular opening in the housing
- ENSURE the board sits flat before tightening screws
- TIGHTEN the screws in the order shown in the picture, using the small torque screwdriver set to 3 in-lb
Control Body Sub-Assembly
[edit]- ATTACH the AKR connector, making sure the tab locks.
- CONNECT the flow sensor wire
- BEND the wires as shown to accommodate cable length
- If the flow sensor is not in the same orientation as shown in the image to the right, it was installed backwards, and needs to be reversed.
- PLACE one #6 x 1/2” Long Type A/AB Tapping Screw into backside enclosure half
- PLACE the backside of the enclosure into a nested condition with the frontside of the enclosure
- TIGHTEN #6 screw using the medium torque screwdriver set to 10 in-lbs while holding the enclosure together with your other hand
- Be careful to avoid any cable pinches!
- PLACE the assembled Flash unit back in the AKR bag, PTC side down
- ISOLATE any failed components immediately. Do not discard.
- Any failed parts should be segregated into the non-conforming bin, and labeled with the date and non-conformance.
- Parts that fail may need to be investigated with the manufacturer by the area engineer.
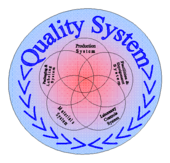
- The content of the document, and every subsequent change, needs to be approved by the team shown below.
- The content should also be reviewed annually for accuracy and applicability.
- Records of reviews are stored and recorded on this Review Sub-Page.
- Training against this document should be preformed annually for relevant employees.
- Records of trainings are stored and recorded on this Training Sub-Page.